- Demand dips: As was the case for many packaging companies discussing the most recent quarter, demand was down, Berry executives said on Thursday’s earnings call for its fiscal Q2, which ended April 1. Inflation and destocking played significant roles. CEO Tom Salmon said that weaker demand resulted in a 6% volume decline, which partially offset other improvement initiatives.
- Restructuring and reductions: Salmon detailed actions to reduce costs and optimize assets. Among them is “rationalizing,” or reducing, 15 facilities across the world and moving business to more efficient facilities. Salmon said one of Berry’s strong points is having “tons of data” to inform decisions on where to shift business to increase productivity, both in terms of consolidating into more modern buildings and moving into different geographic regions. He said a goal is to “shrink that overall footprint without compromising cost or service.” Other facilities beyond the 15 referenced could also be affected, but executives did not offer specific locations. On the flip side, executives announced that Berry’s new U.K. polymers facility recently opened and will be what Salmon called “the world's first closed-loop system to mechanically process, recovered household waste polypropylene back into food-grade packaging.”
- Strategic investments: Over the past few years, Berry has been shifting its investments to higher-growth markets, including food service, health and beauty, and dispensing and pharmaceutical markets. Sustainability-focused projects also are a priority, company executives said. The proceeds from some divestitures will fund growth elsewhere. “We're queuing up these investments to prime the pump, if you will, to make certain that the portfolio is best aligned to support our metrics that we measure ourselves against,” Salmon said. On the food service side, “we continue to see conversion from other substrates to our clear polypropylene cup and lids," said CFO Mark Miles, adding that demand for custom lids has prompted the company to add a Florida manufacturing location.
- Economic outlook: The company anticipates demand challenges throughout 2023, Salmon said. Berry will continue its strategic initiatives and ongoing cost improvements “to exit 2023 a much stronger and more focused company,” he said. Cost-saving initiatives, including facility consolidation, are predicted to provide annualized cost savings of $115 million, with $70 million of the savings realized in FY 2023.

Berry execs talk consolidation, shifting priority sectors
The company is “rationalizing” 15 facilities across the world — and more could be affected — to boost efficiencies and productivity.
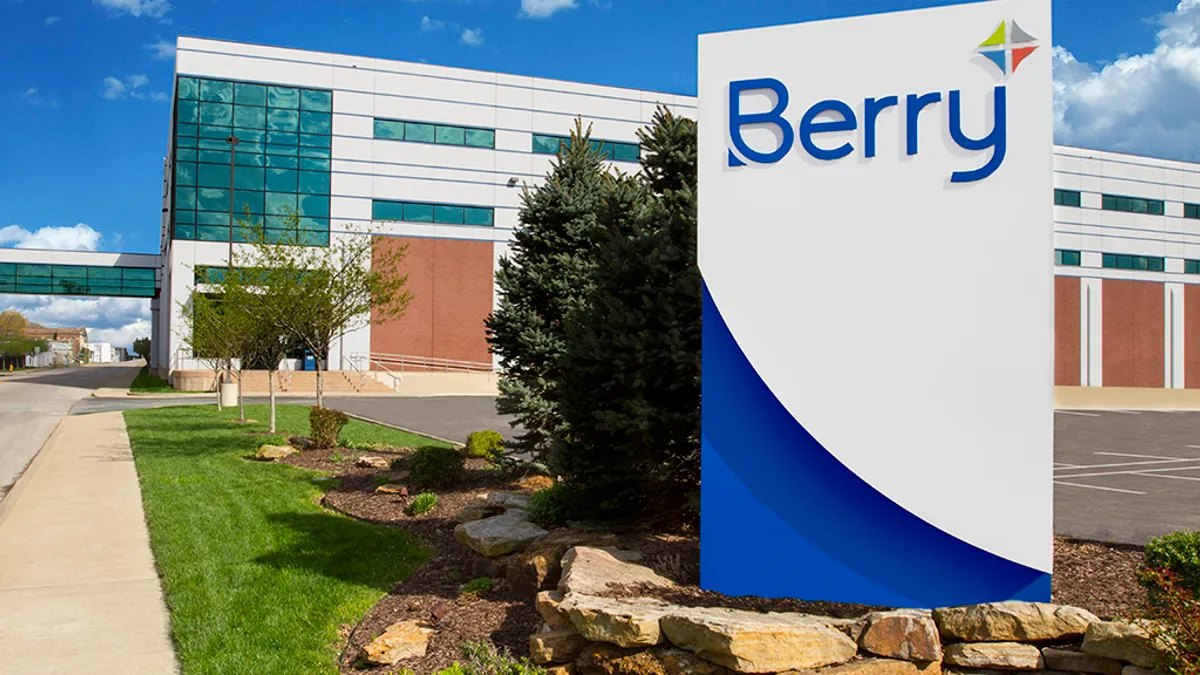
Recommended Reading
- How packaging manufacturers fared in Q1 By Packaging Dive Staff • Updated May 10, 2023