Recycling project collaborators didn’t just talk the talk at the 2025 Packaging Recycling Summit, they walked the walk and shared tangible results from new and ongoing initiatives to transform how packaging is managed.
Teamwork across the supply chain was again an important theme at this year’s event, especially as various players grapple with what impact to expect from new state laws regarding extended producer responsibility for packaging.
These were some of the collaborative projects spotlighted at PRS in Irving, Texas, from June 25-27:
Removing grey area
Speakers repeatedly referenced projects that harness artificial intelligence and data, such as a partnership between investment group Closed Loop Partners and waste analytics company Greyparrot.
Closed Loop works toward circular economy solutions with partners across academia, nonprofits and the corporate world “because we know that one organization cannot drive this important transition alone,” said Kristin Taylor, director of catalytic capital.
The firm invested in Greyparrot in 2022 when it recognized the platform’s potential to recover more polyethylene and polypropylene, and “really for the entire recycling ecosystem,” Taylor said. It’s a tool enabling brand owners to gather data — such as collection data from MRFs — to better understand what happens to their packaging across waste and recycling supply chains and where improvements can be made.
This waste intelligence platform is the first dedicated to brands, said Gaspard Duthilleul, COO at Greyparrot. “We can track this packaging through the sorting centers and the recycling centers. We can see which ones are being sorted correctly and which ones are not.”
The system can recognize up to 111 different waste categories. It’s granular enough to identify individual brands’ packaging, such as which bottles are from the Coca-Cola Co. and which are from PepsiCo. The information is entered into the AI-driven database. “It’s a bit like Google Photo for waste, for innovation,” Duthilleul said of the system, explaining that users can create data filters to gain specific insights to inform changes.
Greyparrot’s system allows users to “unlock a new, unprecedented level of data to improve bale quality, to reduce residue, to reduce waste to landfill, and to provide actionable data that can really make the entire system more efficient, more resilient and more profitable,” Taylor said.
Pouch pick-ups
Baby food brand Once Upon a Farm sells many of its fruit and vegetable blends in flexible plastic pouches, which provide consumer convenience as well as the ability to use high-pressure pasteurization for processing without using heat. But pouches present recycling challenges.
The B Corp is working to improve its packaging in several ways, said Madeline Tien, a sustainability specialist at Once Upon a Farm. This includes design and materials management, such as using less plastic in each pouch and transitioning from a multilayer design to monomaterial polyethylene to improve recyclablility. The brand also leans on its partnerships to solve sticking points, Tien said, pointing to the collaboration with specialty recycling service provider Recyclops.
The partners developed a pouch mail-back program for consumers, which last year resulted in the collection of 120,000 pouches. Recyclops bales the collected pouches and ships them to a third-party processor that deals with hard-to-recycle plastics; the processor transforms the items into plastic pellets for reuse in new products.
Recyclops offers an alternative collection method for consumers who are skeptical about whether the items they put in curbside bins actually get recycled, said CEO Ryan Smith. “It’s a complex supply chain,” he said, noting hurdles such as few end markets for hard-to-recycle plastics. Recyclops’ work also involves connecting processors with brands to develop solutions for these hurdles and identify novel end markets.
“I really can't stress enough how valuable it is for us to be able to have this level of transparency into the process,” Tien said. “Collaboration, especially for us, really unlocks opportunities that wouldn't otherwise be available to us as an emerging brand.”
The partners acknowledge mail-back programs aren’t the sole recycling solution; they’re one option in the broader ecosystem and currently provide a testing ground for more comprehensive solutions down the road. The long-term hope is for these flexible plastic pouches eventually to be accepted curbside, with the take-back program serving as a stepping stone to get there, Smith said. “The beginning isn't the end. Just because we start a program in a certain way doesn't mean that's how the program needs to end.”
Breaking through beverage barriers
Improving beverage container recovery rates, especially to meet growing demand for postconsumer recycled material, also takes collaborative work, according to PRS speakers.
The goal is to “get a lot more [quality] material out of homes,” said Megan Daum, vice president of sustainability at American Beverage. “We need to make sure that we're linking that quality with MRFs that are upgraded.”
But American infrastructure is lacking, and that presents a major barrier to achieving goals, said JD Ambati, founder and CEO of AI-enabled recycling technology company EverestLabs. While adding optical sorters has changed the MRF game over the last five years, such technologies have a long way to go before they’re considered mainstream and markedly move the needle on improving container recovery rates, according to speakers.
“In the world of processing, we had more innovations between the 1900s to 1990s than we had since the 1990s until now,” Ambati said. “I have a lot of respect for our [MRF] operators, because this is a very critical infrastructure that is running with very little modern technology.”
Speakers noted that grants remain available for equipment upgrades through groups like The Recycling Partnership. The Can Manufacturers Institute also offers funding opportunities for companies that wish to upgrade to modern technologies, such as robots.
“I'll fund anything that gets me additional cans captured and gets some upside” in terms of revenue sharing, said CMI President Scott Breen, noting his group’s financial assistance for technologies at waste and recycling services companies Caglia Environmental in California and LRS in the Chicago area.
“Every quarter, I get a very lovely email with my performance report, how many cans each day that robot captured, and my thousands of dollars in a check. And then I go and search for other opportunities” to invest that money, he said.
Ambati explained that sorting robots also can be adjusted to boost recovery of materials other than cans, such as plastics. Daum, looking at the broader industry implications of specific infrastructure investments, noted that “we love all our containers” and “the rising tide floats all boats.”
Beyond equipment investments, beverage brands and packaging manufacturers report working together to improve container capture rates by supporting the introduction of more bottle bills and navigating emerging EPR laws.
“We are working together because [whether] PET, glass [or] aluminum, we all need our material back so we can meet recycled content mandates. But also so we have domestic, resilient supply chains, and so we can make packaging that has a lower carbon footprint,” Breen said.
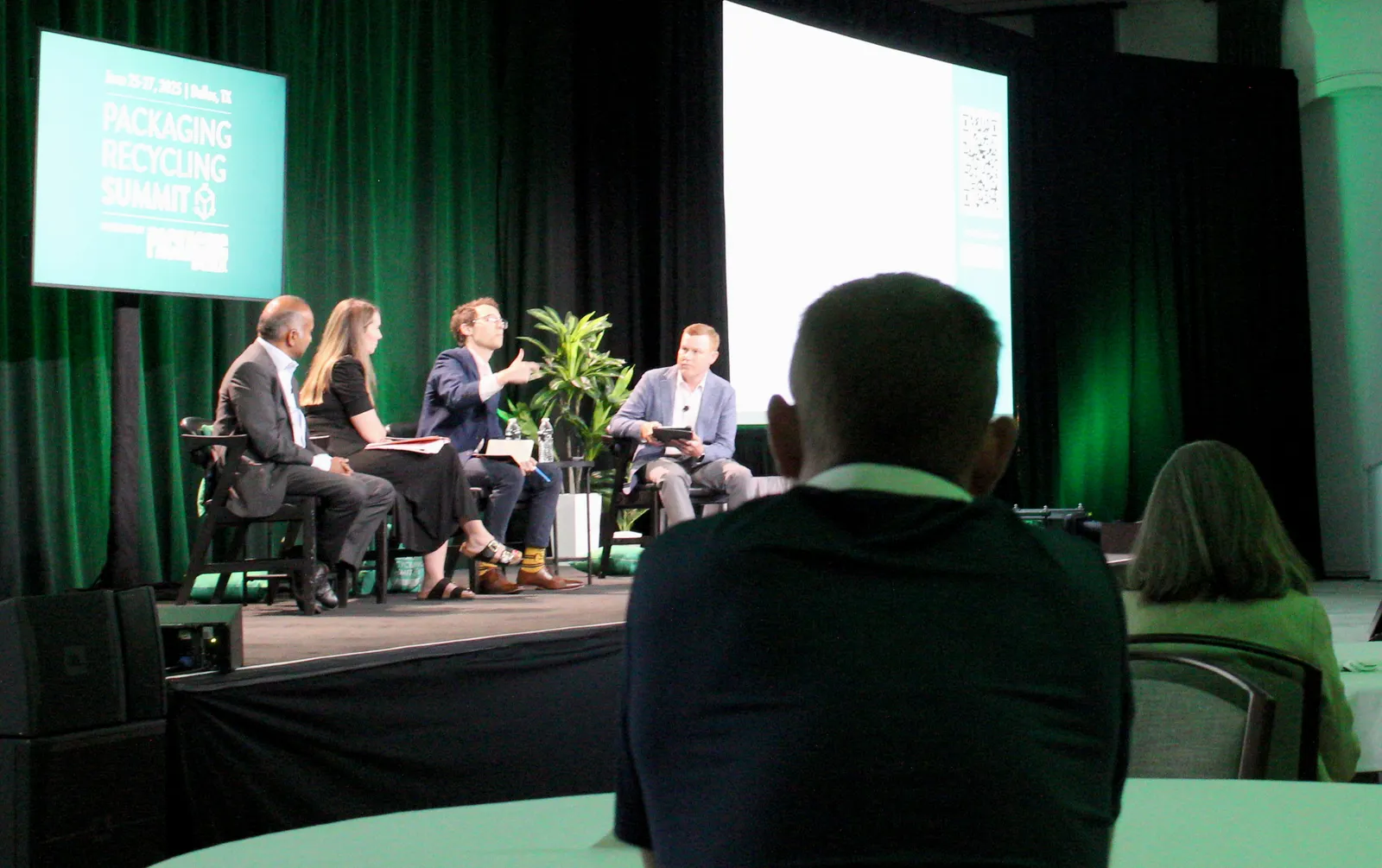
Ramping up research
The Center for Plastics, Paper and Hybrid Packaging just launched thanks to a grant from the National Science Foundation. It’s set up to be a research center that helps to drive packaging recycling innovation and develop skilled workforces by bringing together industry and academia.
“The current administration approving a federally funded and subsidized center in the field of package sustainability is a little bit of a surprise,” said Thomas Osip, industry liaison officer at C3PS. “It’s pretty exciting.”
The goal is to engage not just packaging experts, but also those in fields such as AI, regulatory science and social sciences to collaboratively “work on projects that might be difficult for an individual company, or maybe a little bit risky for them, to tackle alone,” Osip said. The expected output is technologies that enable recycling, as well as solutions for recyclable and compostable packaging.
Member companies will pay a fee to be part of the program. At launch, the initiative’s participants include eight universities, two NGOs and 10 companies, Osip said. Michigan State University is the site hub for the network. C3PS plans to build out its website and operations in the coming months.
C3PS asks industry participants their needs, existing problems and what they wish they currently had but don’t, and then it brings those ideas to researchers who develop project proposals. Some specific areas of interest right now are biodegradable barriers and scalable PFAS-free packaging solutions.
“What's cool about it is industry identifies the needs, industry selects the projects and ... they vote, rank and decide which projects go forward,” Osip said. “Projects get periodic updates. They get results.”