Georgia-Pacific’s integrated paper mill in Brewton, Alabama, is the lone packaging facility among 85 other manufacturing plants that the U.S. EPA recently recognized with Energy Star certification for 2022.
Many of the Brewton containerboard plant’s energy-efficiency improvements are related to its recovery boiler system that generates electricity from natural gas and biofuel residuals recovered during the paper-making process. And Georgia-Pacific isn’t done yet — Brewton is getting another $160 million upgrade this year.
Each year since 2006, the EPA’s Energy Star Industrial Program has certified manufacturing plants that rank in the top quartile of energy performance for their sector. The industrial sector produces 30% of emissions in the U.S., mainly from manufacturing plants’ energy use, according to the EPA. Collectively, the 2022 Energy Star designees saved more than 105 trillion British thermal units of energy and prevented more than 6 million metric tons of carbon dioxide emissions, which the EPA says is equivalent to the emissions from more than 1.1 million U.S. homes’ electricity use.
The journey toward Energy Star certification began when GP’s Brewton plant participated in the Energy Star Challenge for Industry, in which industrial sites are tasked with reducing their energy intensity by 10% in five years. The Brewton plant was recognized as an Energy Star for Industry facility in 2021, the same year it first became Energy Star certified. It was the first integrated paper mill in the U.S. to achieve that distinction, according to GP.
Other GP plants also have been recognized by the EPA for energy efficiency, including paper mills in Green Bay, Wisconsin, and Zachary, Louisiana.
“Our goal was to invest as good stewards of the environment,” said Bob Diercks, optimization of process performance leader at Georgia-Pacific. “We're always focused on trying to get the most out of our resources and have minimum waste.”
Rejuvenating a ‘vintage’ system
GP purchased the Brewton mill, with nearly 500,000 tons of annual board making capacity, from Smurfit-Stone Container Corp. for $355 million in 2007. The facility had been operating since 1957 and received some equipment upgrades in 1964; the newest equipment was installed in the 1980s.
At the time of purchase in 2007, it still contained much of the “vintage technology,” like boilers for chemical recovery and power generation, that were “very inefficient” and prone to outages, Diercks said. “Those were imposing operating costs on the facility that was really dragging it down in terms of its ability to be economically competitive.”
GP has invested $400 million into upgrading the containerboard plant’s legacy equipment and integrating new assets with existing ones. Much of the energy-efficient improvement centers on equipment installed in 2016 and 2017: a modern chemical recovery boiler, a new high-pressure steam turbine, a new chemical evaporator set and associated auxiliary equipment.
“After the first investment, the Brewton mill moved from fourth quartile energy efficiency to second quartile,” said Michael Younis, director of energy optimization at Georgia-Pacific.
The leap in energy efficiency couldn’t have been achieved without the new recovery boiler installation in 2016, but the transformation requires buy-in from the whole team, Diercks suggested.
“We’ve been working with the whole team here to understand the value of energy and how we can minimize the loss,” he said. “The energy consumption in a mill is very heavy — we have water systems, we have steam systems and condensate systems, we have electrical systems — and it really takes everybody here to make that [energy efficiency] happen.”
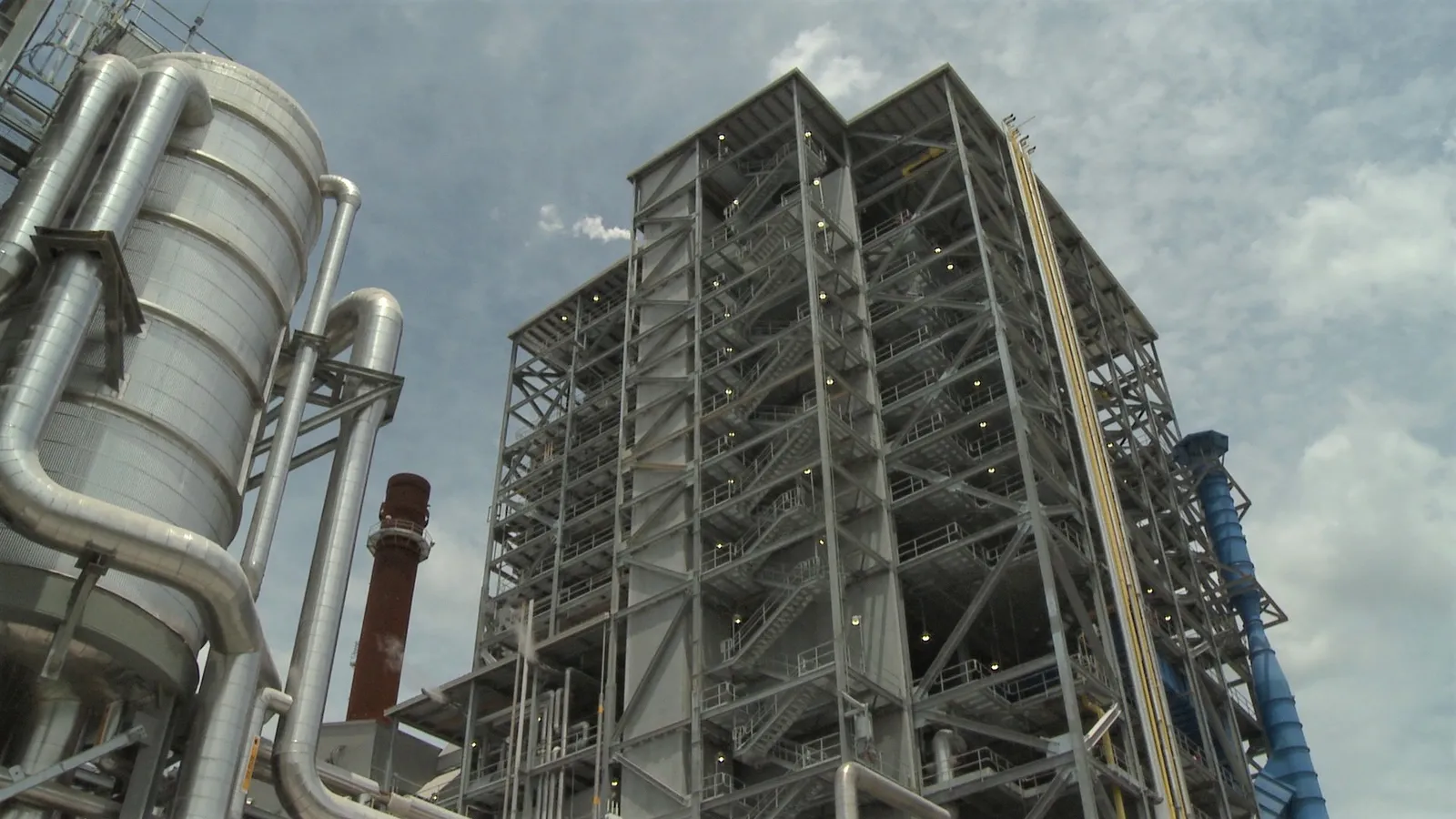
GP’s Brewton facility inputs wood chips as the raw material, turns them into pulp and then produces various board products.
The multi-phase kraft pulping process, through which wood is converted to pulp, is “unique in that we recover the chemicals we use to pulp the wood chips ... We take those chemicals through a recovery boiler and we burn the organics from the trees and that generates the steam to allow us to be very energy efficient,” Diercks said. The steam flows through a turbine to generate electricity “and then we'll take steam off of the turbines at a lower pressure and use that to cook the chips and also to dry the paper that we make,” he said.
“Black liquor,” the leftover chemicals and residues, is processed in a chemical recovery boiler to create “green liquor.” That, in turn, is converted into “white liquor,” a chemical solution used during the first stage of the kraft process.
Pushing further
The $160 million upgrade that began this year on the white liquor plant was not part of what helped the Brewton facility achieve its Energy Star status in 2022, but rather “is the best getting better,” Younis said.
The project involves upgrading the pulp processing systems to further boost the Brewton facility’s energy efficiency, reduce its use of chemicals, reduce other emissions and allow for more paper production. The state-of-the-art technology is estimated to begin operations in spring 2024.
Currently, GP has to buy chemicals for the pulping processes and to convert green liquor to white liquor, and it runs two “very inefficient kilns” that burn gas for chemical conversion. The aged kilns use a lot of energy and produce too much calcium carbonate waste product because the machines aren’t capable of converting it to calcium oxide for reuse. The goal for the white liquor plant upgrade is to increase its capacity and recycle the waste product “over and over and over again in the kraft process, which is one of the things that makes it very economical,” Diercks said.
Georgia-Pacific also monitors energy consumption because it is a big cost driver. And as optimized plants run higher volumes, they become even more efficient, Diercks said. GP’s recent stewardship report notes that its 2021 fuel mix was 54% biogas, 36% natural gas, 7% purchased electricity and 3% coke or coal.
The Brewton plant strives to further improve its kraft process efficiency both when the new white liquor plant opens next year and with optimization measures in the future. The company will track key performance indicators to stay on target.
“The ability to kind of control our own destiny with a lot of our own internal fuel — organic, not fossil fuel — gives us the ability to isolate ourselves a little bit from some of the variability in the market,” Diercks said. “Our year-over-year goal is to stay at that [efficiency level] or gradually improve in that upper quartile to where we're leading the pack in the industry.”