Although some headline-making closures and layoffs have occurred, the packaging workforce generally is in a more positive territory than it was 10 years ago.
A dynamic period of M&A, ongoing labor shortage challenges and effects from the COVID-19 pandemic have left their mark on packaging manufacturers’ staffing levels. Nonetheless, the number of people working at the industry's largest companies increased over the last 10 years, according to calendar and fiscal year reports for 2023.
“On a long run, employment has been growing in some areas,” said Perc Pineda, chief economist at the Plastics Industry Association, explaining that some variances in trends exist among the workforces for different packaging substrates. “But the whole manufacturing industry is decreasing [now].”
Data in securities filings from the top 12 U.S. publicly traded packaging manufacturing companies with annual revenue of $5 billion or greater shows that their collective full-time workforce increased from 2014 to 2023.
The 10 of those companies that existed in 2014 collectively employed more than 212,100 workers that year, and the number rose to a collective 244,800 by the end of 2023. WestRock and Pactiv Evergreen didn't exist in 2014, but when including them in the 2023 total, the count is 315,900.
Packaging manufacturing workforce overall grew from 2014 to 2023
Companies' self-reported data solely considers full-time employees. These data sets do not count temporary hires or contract workers.
While the U.S. Census Bureau also releases data on industries' head counts, the North American Industry Classification System codes they use don't cleanly cover all packaging categories. For instance, NAICS 326140 covers polystyrene foam product manufacturing. That category includes packaging and food service ware, but also foam products that aren't specifically packaging, such as insulation.
Ten years ago, the packaging industry was still recalibrating following job losses that occurred across manufacturing sectors during the Great Recession from 2007 to 2009. While some accounts say the packaging industry fared better than other sectors during that downturn, packaging companies still reduced their capacity in addition to implementing hiring freezes and layoffs. After the recession, product demand ticked up, and so too did hiring.
"The pace of job growth post-COVID was pretty crazy."

Ian Wyatt
Director of commercial economics and commercial market strategist at Huntington Commercial Bank
However, the steady upward trend in leading packaging companies' head counts shifted in 2020. The number of employees dipped that year as large portions of global economies ground to a halt during the COVID-19 pandemic and layoffs ensued.
But soon, stay-at-home culture prompted an e-commerce boom. Packaging employment quickly rebounded as companies scrambled to hire enough workers to fill the robust demand. In fact, overall head count among the top 12 companies peaked in 2021 during the demand surge. It then decreased and plateaued to near 2019 levels for the next two years.
Coming out of the pandemic, more companies have reported investing in technologies and automation, frequently as a way to address labor shortages.
Tracking trends
While broader trends touch most areas of packaging manufacturing, microtrends also are evident in specific sectors. In some cases, these trends appear disparate.
For instance, manufacturing head count overall has decreased in recent years, according to Pineda, but plastic packaging generally experienced growth.
The plastics sector itself can be divided into subsectors, such as film and sheet versus bottles, and some of those sectors’ trends diverged. Employment numbers in film and sheet had a zero compound annual growth rate from 2014 through 2023, Pineda said. The bottle production head count CAGR during that same period was about 1.2%, and 2.7% for unsupported plastic bags.
Plus, individual companies' head count trends varied from the upward aggregate trend, such as International Paper’s drop from 58,000 employees in 2014 to 39,000 in 2023. And some companies’ workforce numbers remained relatively flat instead of showing notable growth or shrinkage. Packaging Corporation of America's head count held steady throughout the entire period, with only a 900-person difference between the start and end points. Sonoco and O-I Glass also showed mostly flat overall numbers.
Many instances of head count growth coincide with business acquisitions over the last 10 years.
For instance, Berry Global's workforce doubled from 2018 to 2019 after the acquisition of RPC Group, and Silgan's head count grew by more than 3,000 people from 2016 to 2017 following the acquisition of WestRock's closures and dispensing systems business unit. Graphic Packaging International's workforce jumped by 5,000 people from 2017 to 2018 following a series of acquisitions, including for Carton Craft Corp., PFP and International Paper's North American consumer packaging business.
Divestitures also played a role, correlating with head count shrinkage. As an example, Berry Global’s head count fell by 2,000 from 2022 to 2023 after it completed a series of divestitures. Some of Berry’s 2022 divestitures include the sale of its plastic rotational molding business to Rotavia and the sale of Synergy Packaging to PACT Group.
“Berry Global unloaded some of those in 2022 ... and had to close some plants. So then you see that there’s this dramatic shift in the number of workers, despite previous years of an increase in head count because they had acquired other businesses,” Pineda said.
Plus, some companies were entirely formed through M&A, such as MeadWestvaco and RockTenn combining to form WestRock in 2015, and Pactiv Evergreen forming in 2020 through the merger of Evergreen Packaging and Pactiv, two Reynolds Group Holdings companies. WestRock later combined with Smurfit Kappa to form Smurfit Westrock earlier this year.
While overall packaging workforce grew from 2014-2023, individual companies' head count trends varied
Pandemic’s outsized influence
Industry observers underscore the significant influence that the COVID-19 pandemic — and what followed — had on overall packaging workforce numbers.
“The pace of job growth post-COVID was pretty crazy,” said Ian Wyatt, director of commercial economics and commercial market strategist at Huntington Commercial Bank, during a session at the Paper and Plastics Recycling Conference on Oct. 23.
For packaging, that time period coincides with the post-pandemic demand boom that prompted record sales at some companies. It was followed by a slump fueled by customers destocking their surplus inventories.
Layoffs bumped up amid that downturn — at least 9,000 layoffs occurred across the packaging industry in 2023 alone, both at public and private companies, with 2024 so far charting similar numbers. A post-pandemic shift in consumer spending from goods to experiences also occurred, which contributed to a decline in jobs numbers, Pineda said.
“If you're still hoping things come back to the way they were before COVID, you've got a problem.”

Doug Larsen
Corrugated market analyst at Green Markets, a Bloomberg company
Several packaging company executives, including Ball CEO Dan Fisher, referenced during earnings calls a demand “trough” in 2023. That October, when asked about unexpected recent closures and layoffs, International Paper's then-CEO Mark Sutton said on an earnings call that “what's changed is the depth and duration of this downturn. It's not like anything we've seen since we built the industrial packaging business starting in the mid-2000s.”
In February 2024, Sutton further detailed workforce changes and reflected on how, in hindsight, he would have reallocated resources earlier.
“During the 2021, '22 period, the workforce started to turn over,” Sutton said on an earnings call. “If I had to do it over, I wish I would have spent much more on physical plant equipment in '18, '19 and '20. ... We got caught a bit there with a change in the workforce.”
Concurrent condition shifts
Other labor conditions evolved rapidly in recent years. Among them, labor shortages cropped up and wage growth surged.
“Since 2015, the bottom 25% of Americans have been getting the biggest raises ... Post-COVID, it was even the bottom half of Americans,” Huntington's Wyatt said, noting that the growth immediately after the pandemic has since slowed. “That's not historically what we're used to. We're not used to white-collar workers being the ones who feel pain, and blue-collar workers not.”
As employee standings strengthened, in part through a series of labor movements in manufacturing and service industries, workers felt empowered to weigh their options and seek positions at other companies that they viewed as upgrades. Thus was born the “great resignation.” The level of “turnover went insane” from 2020 to 2022, Wyatt said, explaining that "those days are over in most spaces.”
During this period, “the traditional manufacturing labor force all of a sudden had options they didn't have before,” such as more lucrative jobs in fast food or warehouses in some states, said Doug Larsen, corrugated market analyst at Green Markets, a Bloomberg company.
E-commerce giants that experienced a pandemic demand surge bumped up their pay rates and often added signing bonuses to attract warehouse and driver recruits. That prompted a migration of some employees who worked in manufacturing facilities with less favorable conditions, like hot box plants without air conditioning, Larsen said. Instead, those employees “could go to work for Amazon or Walmart in distribution centers and get 20 bucks an hour, air conditioned,” he said.
During the pandemic, when Amazon built new warehouses and hired people to work as forklift operators for $35 per hour, "we saw people lured away from box plants for that reason," said Ryan Fox, corrugated packaging market analyst at Bloomberg Intelligence.
Compound that with the post-COVID packaging demand surge when “we overworked our people to try and make up for the excess demand,” Larsen said. “A lot of people said, 'I'm done.' ... Employees were leaving in droves, because we were working our good employees to death."
These factors resulted in a level of churn that especially affected manufacturers that already were running lean operations, Larsen said.
“The training, the onboarding, those programs have evolved in the last three or four years to where the people tell us they're constantly onboarding and constantly training,” he said. “If you're still hoping things come back to the way they were before COVID, you've got a problem.”
Tapping alternatives
U.S. Census Bureau data shows a shrinking overall labor pool. In light of that, packaging manufacturers have turned to a variety of alternative methods to keep their ranks filled — from different recruiting practices to equipment investments.
Many employers are exploring largely untapped employment pools.
“Maybe five years ago, [some companies] wouldn't hire anybody with a felony,” Larsen said, but now more and more packaging manufacturers are hiring formerly incarcerated individuals to fill labor gaps.
Berry Global is among those that have invested in programs to hire refugees. And across the board, there's also a push to get more women to apply for manufacturing jobs, Larsen added.
In addition, the use of automation is increasing, especially among major companies that are driving industry consolidation. Sources say that's connected to workforce head count, but not necessarily in the way many people think. In fact, manufacturers frequently increase their use of automation to bridge gaps in the workforce.
Every manufacturing workforce statistic is getting worse, said Jorge Izquierdo, vice president of market development at PMMI, during a media event at Pack Expo International on Nov. 4. The difficulty with finding workers in general, and especially those with the necessary skill sets, is prompting more companies to fill those voids with technology investments, he said.
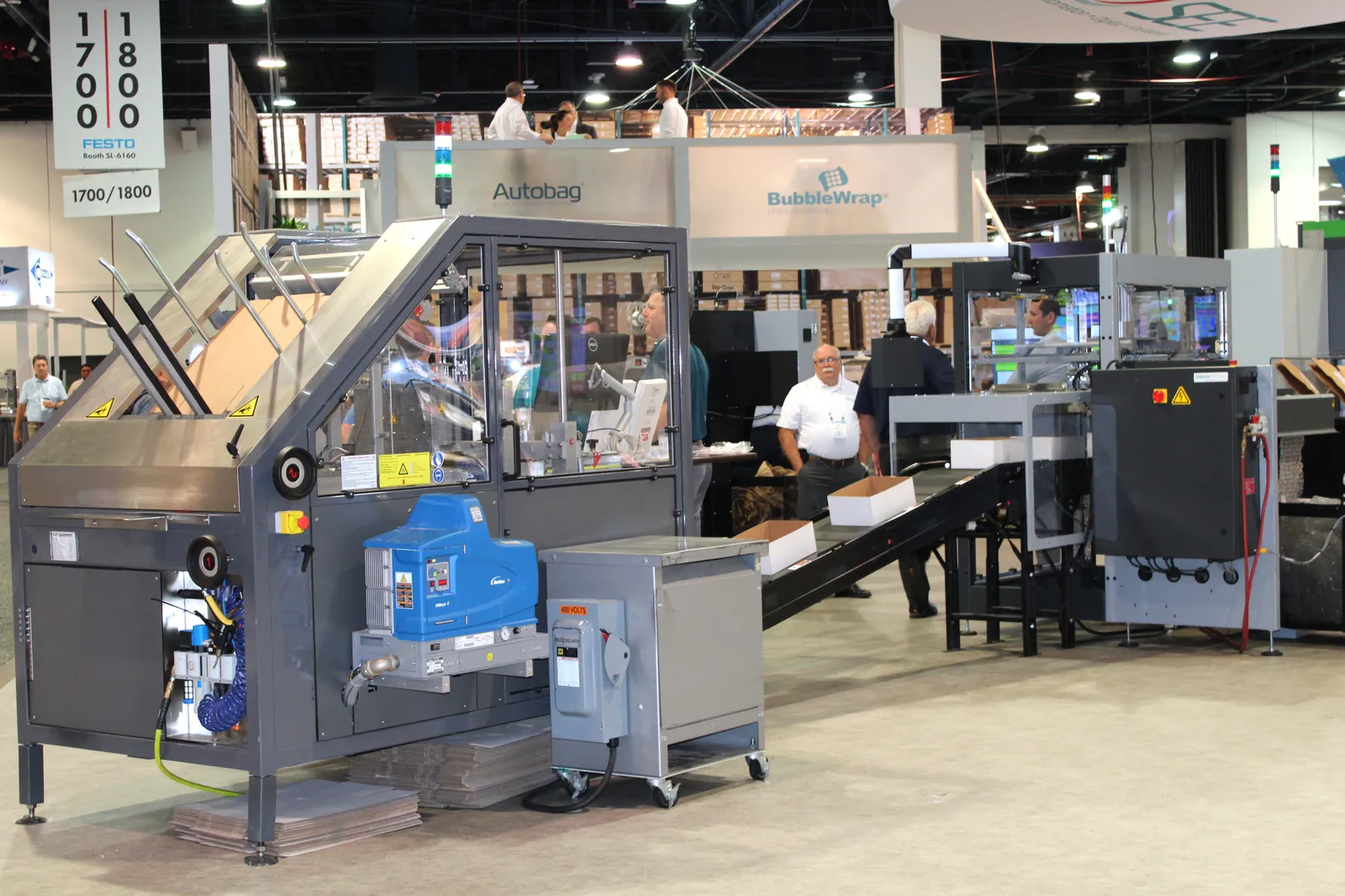
Plus, automation is fitting into more manufacturing spaces as technologies continue to evolve. The number of tasks that can be automated “has changed pretty dramatically in certain categories already, thanks to AI and other technological advances in robots,” Wyatt said.
Some areas might experience short-term pain as workers are indeed cut in favor of machines, he said. But in the long term, more automation creates new opportunities to upskill workers to operate modern equipment in higher value positions while the machinery performs the repetitive work, Wyatt explained.
“Historically, we've been through these periods where people get scared about innovation," he said. However, historic data shows automation "often creates jobs. People get reallocated."
For instance, box plant managers may now invest in reskilling workers, not necessarily cutting them, as they add automation, Bloomberg Intelligence's Fox said.
"They upskill some of those people and say, 'We don't need you doing the stacking. We need you to know how to man the robot and to make sure the robots are functioning properly,'" he said. "So that person gets a better job without losing any workforce."
Larsen concurred that "there's been a tremendous amount of investment" in the corrugated industry in areas such as "new high-speed corrugators, new high-speed converting, more conveyors, more robotics."
Plastics' Pineda agreed that innovation can positively influence head count over the long term. "In areas where there's more of an increase in spending on R&D, then you'll probably see an uptick in employment," he said.
At least for the short term, the trend toward packaging companies making technological investments to supplement human labor is expected to continue.
"There's no expectation that the workforce situation will be improving significantly in the near future, so you need to plan for it," Izquierdo said, pointing to a "significant push, significant investment" in new technology "to alleviate all these problems."